By Abigail Cloutier
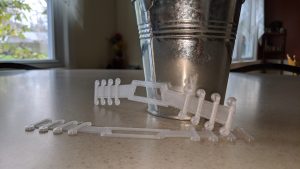
A 3D printer, open-source blueprint and over 1,000 face mask straps are how Youngstown State University senior John Galvin is using his time in self-isolation.
The information technology major is giving the mask straps, which are designed to relieve pressure from the wearer’s ears, to essential personnel for free. He’s spent countless hours printing, sanitizing and shipping the flexible plastic straps.
“Currently, it is just me [printing the straps]. No one is helping me,” he said. “I actually bought a second 3D printer to keep up.”
Due to the demand, he has temporarily stopped taking requests, but Galvin has received orders from Ohio, Pennsylvania, several states in the Midwest and even an individual in Florida. Both individuals in essential fields and department heads have made requests from as little as two straps to over a hundred.
“I sanitize them and ship them out as soon as they’re done printing,” Galvin said.
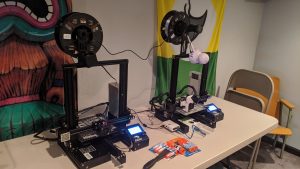
He makes at least one trip to the post office per day. Currently, he is covering the cost of sanitizing the straps, postage and 3D printer filament himself, but he has created a GoFundMe fundraiser to help with the cost.
“The filament [rolls] are about $20 apiece, and I’m not positive about how many I can get out of one,” he said. “A few hundred would be my guess.”
Jennifer Nance works for Kemper House, a company that manages several long-term care and assisted living facilities in northeast Ohio. Every employee is using the mask straps donated by Galvin.
“It’s uncomfortable wearing a mask all day, and it rubs behind your ears,” Nance said. “It can be really irritating.”
Many of her employees work eight-hour shifts without taking off their masks.
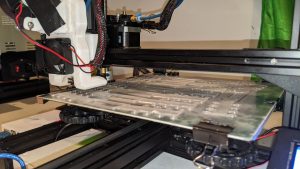
“Not only do the bands that John made help prevent that, but it also helps the mask fit better and more snug to your face. There’s less chance of air or germs getting through the sides,” she said.
Nance also noted that the straps are very easy to sanitize and reuse since they are printed from plastic.
Tom Reed is the station manager and paramedic supervisor at EMT Ambulance in Warren. It is one of the largest ambulance providers in the area and responds to emergency calls and medical transfers between hospitals.
“Before COVID-19, the biggest risks were hepatitis and AIDS,” he said. “But that’s transmitted pretty much from blood-to-blood contact. With COVID, we have to treat pretty much everyone like they’re infected.”
Reed’s EMTs work 24-hour shifts on and then have 48 hours off. During that 24-hour shift, they are always on call.
“Across the board, I made it mandatory to wear a mask and gloves, bare minimum, on call,” he said. “If we have calls that are shortness of breath, fevers, anything that has COVID symptoms, we’re going with goggles, gowns, gloves and masks.”
Reed estimates that the company is going through 40 to 60 times the number of personal protective equipment than it did prior to the pandemic.
“These clips, they are adjustable and strap behind your head instead of your ears, so you really can’t feel that you’re wearing a mask,” he said.
Reed stressed the importance of safety during this time.
“This disease is invisible. [We’re] fighting an invisible enemy,” he said.
Cutlines for photos: Galvin’s 3D printers melt and extrude plastic filament to create the mask straps.